I'm a big fan of ducks, evidenced here with an entire page dedicated to the wonderful little creatures. From their surprising flight capabilities to their quick-kicking flippers, I've always marveled at their splendor.
This is the first stage in building a remote controlled duck. The duck will float atop a body of water, propelled only by oscillating flippers.
The flippers fold to become streamlined when moving forwards, but expand while moving in reverse. Placed underwater, this simple oscillation should produce forward thrust, similar to a duck's feet.
Steering is achieved through differential control of the flippers. They move independently, and are controlled remotely through an rc transmitter.
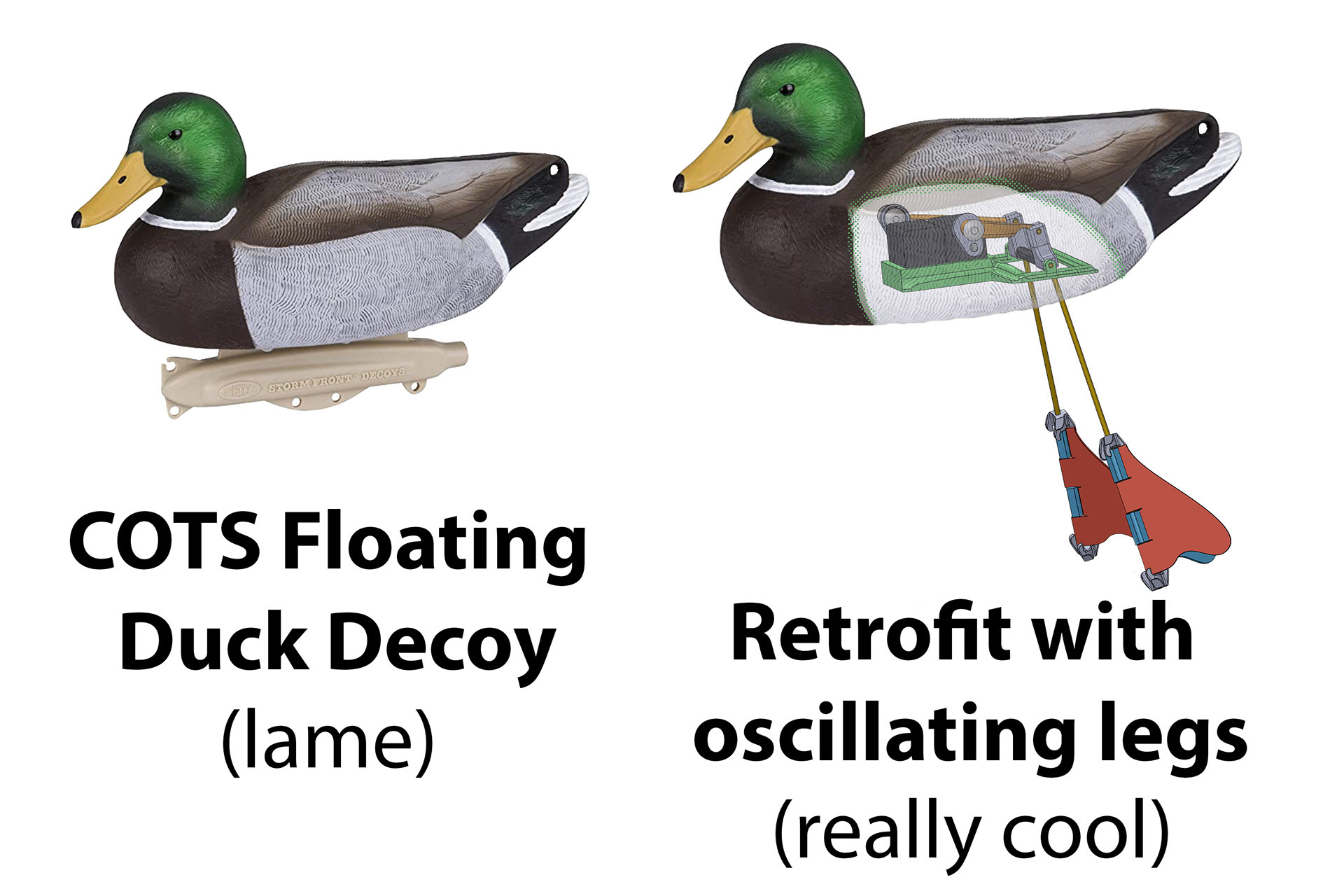
The first step for me was figuring out what kind of motors would best perform this oscillating motion. The motors do not need much speed, but rather should have high torque and fine-tuned control. This is because a duck's legs do not oscillate very quickly. At most, the motors would need to run at around 100rpm.
For these reasons, and because I wanted to learn more about stepper motors, I first chose a very compact stepper motor for this project, linked here. In order for these motors to function with my RC transmitter, I also purchased this tic motor controller.
Each motor was connected to a separate TIC controller, each of which were then linked to a control stick on my RC transmitter. This means that I can control the speed of the motors individually, allowing the duck to kick each leg independently!
Here is a crude bench test demonstrating the differential control of the flippers, as well as the folding structure of the flippers themselves. They are designed to fold and minimize drag while the flipper moves forwards, but expand to push water backwards on the backswing. This is a very early prototype, so the motion is quite robotic and linear. I'm hoping to add some more joints in the legs to help smooth out each stroke. For now though, this serves as a proof of concept.
During this bench test, I also realized that my motor selection was severely under torqued. Even the slightest amount of friction or resistance on the flippers was enough to halt the small stepper motor. This issue will be resolved with higher torque motors!
The flipper actuation design and parts were all designed in Solidworks and then 3-D printed for prototyping. The photo on the right shows the assembly view for motors and oscillator structure. With this design, I am able to adjust the maximum sweep angle each leg travels through, and the design is compact enough to fit inside a duck!
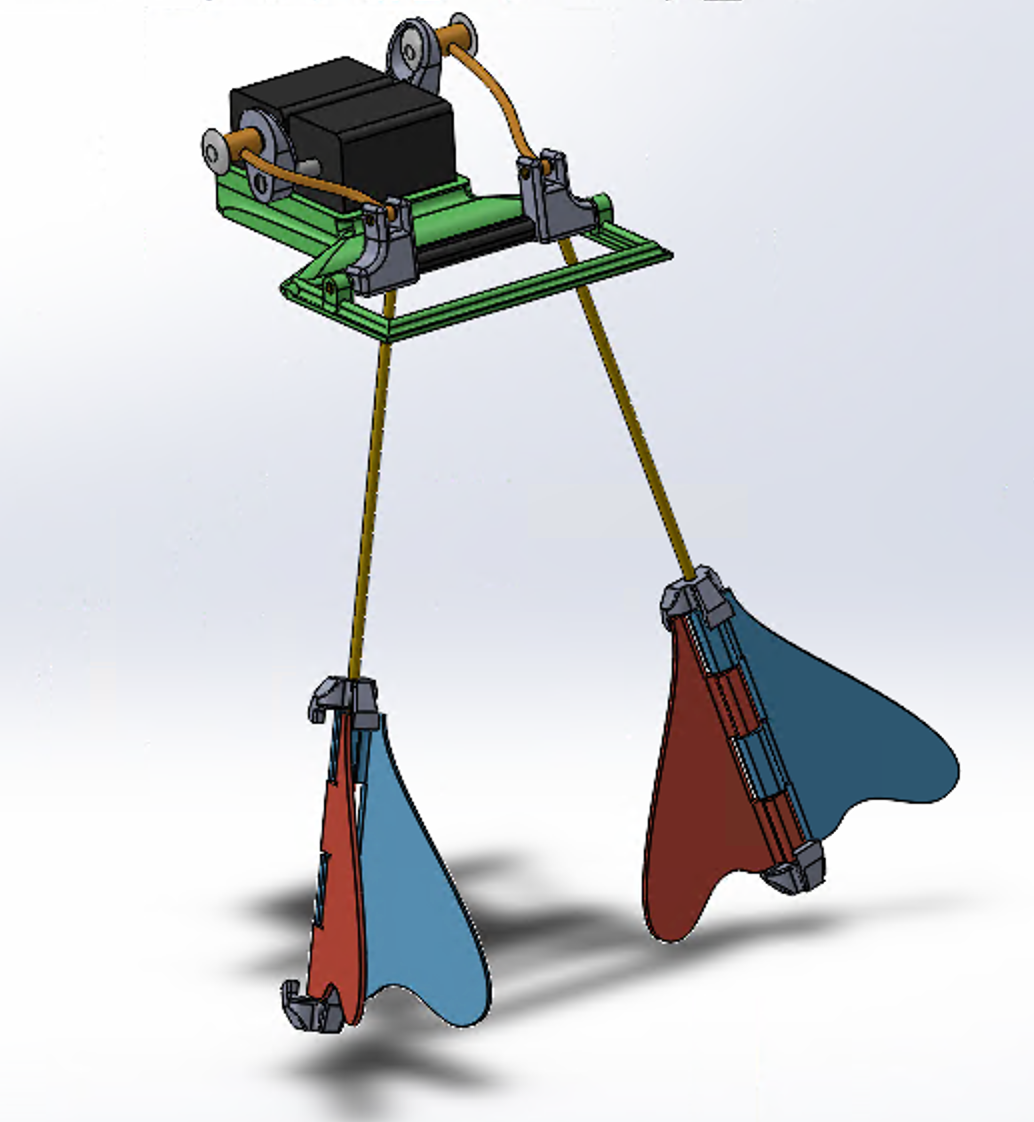
This project has not been finished yet, I'm awaiting a delivery of some high-torque replacement motors. When they arrive, I'll be reconfiguring the assembly, and then hopefully mounting it inside of a duck decoy that I've hollowed out! Check back later for updates!